如何建立高效低成本洁净钢平台
刘 浏
(钢铁研究总院, 北京 100081)
作者简介:刘 浏(1951—), 男, 博士, 教授; E-mail:liul@cisri.com .cn ; 收稿日期:2009-09-23
作者介绍访问本站洁净钢专家专栏中介绍:
刘浏-钢铁研究总院总工程师
摘 要:根据洁净钢的定义, 阐明了建立洁净钢制造平台的重要意义, 分析对比以铁水“三脱” 预处理为基础的洁净
钢生产新流程和以炉外精炼为主体的传统流程的技术指标。 讨论了传统洁净钢流程中存在的炼钢回硫、低碳脱
磷、脱氧与夹杂物控制和强还原精炼等 4 项基本矛盾, 并讨论其对洁净钢生产成本和能耗的影响。 在此基础上提
出建立高效低成本洁净钢平台应重点研究解决全量铁水“三脱” 预处理、少渣冶炼、高碳出钢和真空碳脱氧以及改变夹杂物上浮方式等 4 项关键技术。
关键词:洁净钢;转炉;铁水预处理;炉外精炼
中图分类号:TF 71 文献标志码:A 文章编号:0449-749X(2010)01-0001-09
A Proposal to Establish a Platform for Manufacturing High-Efficiency and Low-Cost Clean Steel
LIU Liu
(Central Iro n and S teel Resea rch I nstitute , Beijing 100081 , China)
Abstract:Acco rding to the definition of clean steel, a g rea t sig nificance in establishing a clean steel manufacturing platform is clarified.The technical index of new pr oductio n pro ce ss of clean steel based on ho t me ta l pretreatment is analyzed and compared w ith that o f traditional pro ce ss of taking seco ndary refining as main body .I n traditional process, there are fo ur ba sic co ntradictions such as resulfurizatio n, de phospho rization in melting low carbon steel,deo xidizatio n and inclusion contro l, and stro ng reducing refining , w hich hav e an influence o n production co st and e nergy co nsumption .To so lve there pr oblems, a platform fo r manufacturing hig h-efficiency and low-co st clean steel should be established .The platform must focus on full ho t me tal pretr eatment , le ss-slag smelting , high-carbon taping, vacuum car bo n deox idization and chang e of inclusio n floa ting , and so on .
Key words:clean steel;converte r;ho t metal pret reatment;seco ndary refining
洁净化是现代钢铁材料发展的主要潮流, 洁净钢生产是当代炼钢技术发展的重大方向 。欧美国家采用传统流程生产洁净钢 ,其特点是以炉外精炼作为控制钢水洁净度的主要手段, 采用铁水脱硫预处理—转炉冶炼—炉外精炼工艺。日本开发的洁净钢生产新流程强调采用全量铁水“三脱”预处理工艺 ,实现转炉少渣冶炼 , 通过铁水预处理控制钢水洁净度 , 达到降低成本和提高效率的目标 。
目前 ,世界金融危机使全球钢铁业进入萧条时期,如何降低洁净钢制造成本 、降低能耗和减少制造过程中的环境污染成为今后全球钢铁业市场竞争的焦点 。为此,迫切需要建立起高效低成本洁净钢生产技术平台。
1 洁净钢与洁净钢制造平台
“洁净钢”最早由欧洲学者于 20 世纪 60 年代提出 ,专指通过严格控制钢中夹杂物提高钢材强韧性和塑性的工艺方法 。20 世纪 80 年代日本学者进一步提出“纯净钢”的概念 , 将钢中夹杂物与杂质总量结合起来,并定义 ∑w(S +P +N +TO +H)≤100 ×10-6的钢为纯净钢, 同时提出建立大批量、低成本、稳定生产纯净钢的技术平台 。
必须指出 ,洁净钢或纯净钢并非特指某一类具体的钢种,而是代表实际生产过程中控制钢水洁净度所能达到的工艺水平。因此, 洁净钢不是一个钢种的概念,而属于生产工艺范畴 ,反映出洁净钢具体的生产工艺和制造水平 。
表 1[ 1] 给出日本学者 20 世纪80 年代末和90 年代初对 21 世纪国际洁净钢制造水平的预测及其现实所能达到的工艺水平。从表中可以看出 ,当时对钢水 w([ C] )的预测水平为(4 ±0 .2)×10-6, 而实际上已能稳定生产 w([ C])≤3 ×10-6, 超出预测水平 。这主要得益于真空精炼中进一步扩大界面反应速度所取得的工艺效果。表中 w([ S] )和w([ O] )的实际水平与预测水平基本相近,但[ P] 和[ N] 的制造水平尚与预测水平存在较大差距, 说明这些元素
的提纯工艺仍需进一步研究开发 。
国内习惯采用“洁净钢”反映生产过程中钢水洁净度的控制水平 ,从表 1 可以看出国内洁净钢制造水平和国际先进水平相比尚存在一定的差距 。建立高效低成本洁净钢平台其目的就是要优化洁净钢冶炼和精炼工艺, 在提高钢水洁净度的前提下进一步提高生产效率, 降低洁净钢制造成本。
2 两种洁净钢制造流程
2 .1 传统流程
传统洁净钢制造流程如图 1 所示 , 主要采用铁水脱硫预处理 —传统复吹转炉冶炼 —LF 炉精炼与RH 真空精炼 —全连铸生产工艺, 可以生产出高洁净度的钢水 。但由于工艺流程长, 生产工艺和原辅材料的波动造成钢水质量不稳定;钢水提纯主要依靠炉外精炼 ,造成能耗高、成本高 、CO2 排放量高。
2 .2 日本新流程
日本学者认为:传统洁净钢生产流程存在着生产成本高、能耗高、CO2 排放量大和产品质量不稳定等缺点。为改进这些缺点, 提出采用“ 分阶段冶炼”工艺 。经过 20 年的发展完善, 形成了洁净钢制造新流程,如图 2 所示 。其特点是采用高炉低硅冶炼和铁水脱硅预处理 ,严格控制硅含量—全量铁水“三脱”预处理 —转炉少渣冶炼 —高碳出钢和 RHKTB 热补偿—全连铸工艺。

新流程的主要技术优点:
1)减少渣量,比传统流程减少渣量 40 %~ 60 %;
2)缩短转炉冶炼周期 30 %~ 50 %;
3)减少吨钢铁耗 15 ~ 20 kg ;
4)减少吨钢铝耗 1 .5 ~ 2kg , 对不同钢种可降低铁合金消耗 3 ~ 10 kg 。
2 .3 两种流程的比较
表 2 给出传统洁净钢流程与日本洁净钢生产新流程的比较 ,从表中可以看出新流程转炉钢水的洁净度明显高于传统流程 ,而生产效率 、消耗指标和生产成本均比传统流程降低 ,具有明显的技术经济竞争力。
表 2 传统洁净钢流程与日本洁净钢生产新流程的比较
Table 2 Comparison between traditional manufacturing process and Japanese new manufacturing process of clean steel

3 传统流程的基本矛盾
传统洁净钢生产流程中存在着炼钢回硫、低碳脱磷 、铝脱氧与夹杂物控制及强还原精炼 4 项基本矛盾 ,是造成洁净钢生产不稳定、能耗高、成本高和CO2 排放量大的重要原因。
3 .1 炼钢回硫
炼钢回硫是传统洁净钢生产流程中存在的主要问题 ,不仅造成钢水质量波动 ,而且大幅度增加生产成本 。炼钢回硫的主要原因如下。
1)铁水硫含量低, 回硫趋于严重。铁水脱硫预处理工艺具有良好的热力学条件 ,渣钢间硫分配比超过1 000 , 目前可以稳定生产 w([ S] )≤20 ×10-6的低硫铁水(如 K R 法)。
2)转炉炼钢过程使钢水和炉渣氧位升高, 渣钢间硫分配比降低到 2 ~ 5 ,如图 3 所示, 钢水易被炉渣污染造成回硫。如石灰 w([ S] )为 0 .02 %, 铁水w([ S] )为 20 ×10-6 时转炉冶炼终点与炉渣中石灰带入的硫平衡的钢水 w([ S] )为 40 ×10-6,回硫率100 %。说明生产超低硫钢石灰硫的质量分数必须小于等于 0 .01 %,否则就会污染钢水,形成回硫。
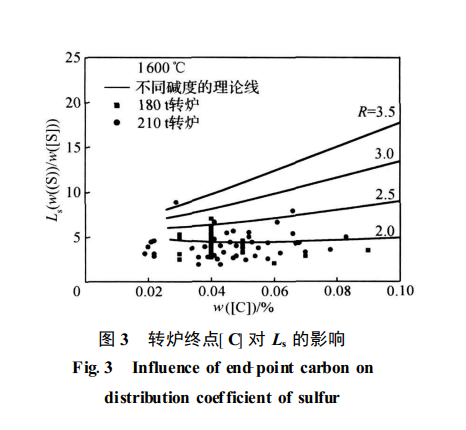
炼钢回硫造成的危害非常严重 ,主要表现为:
1)要求大幅度降低废钢 、石灰和其他原辅材料的硫含量 ,增加生产成本 ;
2)需采用 LF 炉二次脱硫 ,增加脱硫成本;
3)LF 炉脱硫生成大量 Al2O3 二次夹杂 , 难以碰撞聚合 ,上浮分离 。
3(CaO)+3[ S] +2[ Al] =3(CaS)+(Al2O3)
提高渣钢间硫的分配比是抑制转炉炼钢回硫的技术关键。如表 3 所示 ,在铁水脱磷预处理过程中,采用低氧位脱磷工艺 , 适当提高炉渣碱度和降低渣中 TFe 含量 ,渣钢间硫的分配比提高到 20 ~ 30 , 可抑制炼钢回硫。

3 .2 低碳脱磷
低碳脱磷是转炉炼钢的主要特征 , 为了保证脱磷,要求提高钢水氧位, 使钢渣过氧化 。
如图 4[ 2] 所示,随着终点[ C] 的降低转炉渣钢间磷的分配比提高,增加底吹喷嘴数量(提高喷嘴出口线速度)有利
于提高渣钢间磷的分配比 。
造成转炉低碳脱磷的技术原因是:
1)[ C] 高时 ,氧传质决定熔池碳氧反应, 熔池氧位低 ,难以保证脱磷所要求的氧位 ;
2)吹炼中期难形成高碱度炉渣 ,抑制了脱磷反应;
3)终点温度高 ,降低了渣钢间磷的分配比。低碳脱磷造成的危害主要表现为:
1)反应温度高造成脱磷效率低 ,渣量大 ,如表 4所示 ;
2)钢水过氧化 , 无法实现高碳出钢, 增加了脱氧铁合金成本和去除夹杂物的困难 ,如图 5 所示;
3)脱磷铁耗高 ,脱磷成本大幅度提高。
解决措施是采用铁水脱磷预处理工艺, 提高脱磷效率;采用低 FeO 渣脱磷工艺 ,降低铁耗 ,同时可抑制脱磷预处理过程中半钢增硫 ;严格控制铁水硅含量,减少渣量。
3 .3 铝脱氧与夹杂物控制
铝强化脱氧是传统流程采用的最主要脱氧方法,可以保证钢水的洁净度,但也带来了夹杂物控制的难题。

采用铝脱氧后产生大量 A l2 O3 夹杂难以上浮去除 ;精炼过程中铝不断还原渣中 FeO 、SiO2等杂质,不断产生零星的 Al2O3 二次夹杂, 难以聚合,上浮困难;铝脱氧降低了钢水流动性, 需采用钙处理 工艺 。如 图 6 所示, 控 制钢 中 w ([ Ca] )/w([ TO] )大于等于 2 才能保证形成球状氧化物, 利于上浮去除。

传统流程中控制钢中夹杂物常采用的工艺方法是:
1)出钢大量用铝沉淀脱氧;
2)精炼过程采用铝扩散脱氧 ,降低炉渣氧位 ;
3)采用高碱度 、高铝钙比渣系提高炉渣吸附Al2O3 夹杂的能力 ;
4)为保证夹杂物充分上浮需采用长时间弱搅工艺 ;
5)为保证钢水流动性 ,需要进行钙处理;
6)完成以上工作 ,大幅度增加了钢水精炼成本。
解决措施是尽量避免钢水过氧化, 减少铝加入量 ,提高铝脱氧的收得率;尽可能采用真空碳脱氧工艺 ,减少 A l2 O3 脱氧产物对钢水的污染;改变 A l2 O3上浮机制,缩短弱搅时间;优化钙处理工艺 。
3 .4 强还原精炼
为了保证钢水脱硫和控制钢中夹杂物形态 ,降低钢水氧位, 传统洁净钢流程常采用 LF 炉进行强还原精炼,保证钢水洁净度 。
强还原精炼带来的主要技术问题如下 。
1)铝消耗高 ,需要用大量铝脱除钢水和炉渣中的氧。
2)为降低钢中 TO 需用铝还原渣中 SiO2 ,提高炉渣碱度。
3)为改变夹杂物形态需采用高碱度、高 A l2 O3渣系,增加渣量。
4)铝脱氧产生的大量一次和二次夹杂污染钢水 , 并延长精炼时间。例如钢液中每脱除 100 ×10-6的[ S] 需消耗 56 .25 ×10-6 的[ A l] , 生成 106 ×10-6的 Al2O3 夹杂 ;每还原渣中 1 %的SiO2(按渣量10 kg 计算)消耗 60 ×10-6 的[ Al] , 生成 112 .6 ×10-6的 Al2O3 夹杂 。如图 7 所示, 在 LF 精炼前 ,钢水脱氧后产生的一次夹杂物大量上浮, 钢中各种尺寸的夹杂物数量较少。但在 LF 精炼中和精炼后钢水中各种尺寸的夹杂物均有明显的增加 , 说明精炼过程中产生的二次夹杂对钢水造成严重污染。钢中悬浮的大量二次夹杂需要通过长时间的吹氩弱搅或在真空精炼中弱搅才能得以有效地去除。

5)为满足强还原精炼的要求, 明显增加了精炼成本 。
解决的措施主要是提高转炉终点碳含量, 降低钢水氧化性;采用真空脱碳脱氧工艺降低加铝前钢水氧含量 ,提高铝脱氧回收率 ,避免产生大量 Al2O3夹杂 。同时,应进一步改善夹杂物上浮机制, 缩短软吹时间,优化钙处理工艺 。
4 建立高效低成本洁净钢平台的关键技术
4 .1 采用铁水“三脱”预处理工艺
推广采用铁水“三脱” 预处理工艺, 将钢水提纯的重点从炉外精炼转移到铁水预处理是降低洁净钢水成本 ,提高生产效率的技术关键,必须给予高度重视 。
采用铁水“三脱”预处理工艺的技术难点在于能否实现转炉高效脱磷 。脱磷反应是在渣钢界面上发生的氧化反应 , 适当控制炉渣成分, 使渣中 γP2O5 ≤10-17时才能保证脱磷氧位低于脱碳氧位 ,实现高效脱磷和抑制熔池脱碳 。图 8 给出铁水脱磷预处理过程中渣钢间磷的分配比与炉渣碱度和渣中 FeO 间关系。从图中可以看出 ,随着炉渣碱度的升高, 渣钢间磷的分配比升高, 有利于熔池脱磷 ;而渣中w(FeO)在 5 %~ 40 %范围内变化对渣钢间磷的分配比影响较小。因此, 如何在铁水预处理的低温条件下尽快形成高碱度炉渣是提高脱磷效率的技术关键。

铁水脱磷预处理过程中由于熔池碳含量高, 半钢水氧位低,有利于抑制炼钢回硫 ,对转炉洁净钢生产具有重要意义 。转炉脱磷预处理过程中为保证热平衡需要加入大量废钢 , 同时脱硫铁水中残余的高硫渣和造渣剂带入的硫含量增加了预处理过程中的硫负荷 。为抑制回硫 , 唯一的途径是努力提高渣钢间硫的分配比,如图 9 所示 ,在脱磷预处理过程中控制炉渣 w(FeO)≤8 %有利于迅速提高渣钢间硫的分配比 。因此,采用低氧化铁炉渣脱磷预处理工艺,控制合适的炉渣碱度(R ≥2 .5)和渣量(w((S))≤0.06 %)可以将渣钢间硫的分配比提高到 20 ~ 30 ,从而解决炼钢回硫的技术难题。

为了降低转炉脱磷预处理的生产成本, 提高脱磷预处理过程中的脱磷氧效率 ηO2 和石灰效率 ηCaO是十分重要的 。严格控制铁水 w([ Si] )≤0.3 %可使脱磷预处理氧耗降低到每吨钢 10 ~ 12 m3, 进一步提高渣中 3CaO · P2O5 和 4CaO · P2O5 比例, 可达到提高脱磷石灰效率 ηCaO 和降低脱磷渣熔点的目的[ 3] 。
4 .2 实现转炉少渣冶炼
大量的生产实践证明转炉少渣冶炼具有以下冶金特点 :
1)碳氧反应更接近平衡, 减轻了钢水过氧化趋势;
2)熔池脱碳速度快, 熔池碳氧反应由氧扩散控制转变为碳扩散控制的临界碳的质量分数由 0 .6 %降低到 0 .15 %,有利于避免钢渣过氧化 ,如图 10[ 4]所示;
3)渣钢间脱磷、脱硫反应效率进一步提高 ;
4)如 图 11[ 5] 所示, 实现锰矿 熔融还原 , 当w([ C] )≥0 .08 %时锰收得率高达 90 %;
5)钢水 洁 净度 高:w ([ N ] )≤15 ×10-6,w([ H] )≤1 .5 ×10-6 。

实现转炉少渣冶炼的主要工艺措施如下。
1)降低脱磷炉渣量。传统造渣理念根据铁水[ Si] ,按照终渣碱度要求确定渣量;先进的造渣理念应根据铁水[ P] 控制渣量, 通过适当控制铁水硅含量和提高渣钢间磷分配比实现少渣冶炼 。如图 12所示 ,在铁水初始 w([ P] )为 0 .1 %和半钢 w([ P] )为 0 .01 %的条件下,控制渣钢间磷分配比为 800 , 渣中 w (P2O5)达到 8 %, 要求控制初始 w ([ Si] )为0.18 %,脱磷炉总渣量每吨钢仅为 26 kg 。若渣钢间磷分配比降低到 150 ,渣中w(P2O5)降为 3 %, 铁水
初始 w([ Si] )可控制在0 .5 %,脱磷炉总渣量每吨钢增加到 68kg 。降低脱磷炉渣量对减少石灰消耗和降低铁耗 、提高钢中残锰含量具有重要的经济意义 。
2)实现脱碳转炉少渣冶炼。考虑到脱碳转炉溅渣护炉的要求, 应控制脱碳转炉渣量每吨钢在20 ~ 25kg , 每吨钢石灰加入量为 10 ~ 15kg 。转炉采用少渣冶炼可避免渣料对钢水回硫的影响, 并可实现锰矿熔融还原。一方面有利于炉渣熔化, 另一方面可节约锰铁合金消耗 ,对降低炼钢成本有重要意义。

4 .3 高碳出钢与真空碳脱氧
采用铁水“三脱”预处理和转炉少渣冶炼工艺后 ,解决了转炉低碳脱磷的技术难题 ,可以实现高碳出钢。为避免钢渣过氧化 ,生产低碳钢应将转炉出钢 w([ C] )稳定在 0 .06 %~ 0 .08 %, 钢中 w([ O] )从(800 ~ 1 000)×10-6 降低到(300 ~ 400)×10-6 ;生产中、高碳钢应将转炉出钢 w([ C] )提高到 0 .3 %以上,使钢中 w([ O] )降低到 100 ×10-6以下。这对于大幅度减少脱氧铝耗和脱氧生成的 A l2 O3 夹杂总量具有重要意义 ,有利于提高铝脱氧的收得率 ,降低钢中夹杂物总量 。对于需要采用真空精炼的钢种 ,应采用真空碳脱氧工艺, 进一步降低脱氧夹杂物, 提高钢水洁净度 。采用真空碳脱氧具有以下优点:
1)真空碳脱氧, 脱氧产物为气体 , 不会污染钢水 ;
2)真空有利于碳氧反应 , 达到理想的脱氧效果 ;
3)真空碳脱氧可大幅度降低脱氧和去除夹杂物的成本。
实现真空碳脱氧的工艺措施 :
1)采用沸腾出钢工艺, 减少钢水增碳量, 避免出钢过程中吸氮、吸氢 ,造成钢水污染 ;
2)适当提高转炉终点 w([ C] ), 实现 RH 或VOD 真空精炼过程中的热补偿;
3)优化 RH 工艺参数 ,促进碳氧反应平衡 ;
4)提高铝深脱氧的收得率 ,减少铝耗。
图 13 、14 给出传统脱氧工艺和真空碳脱氧工艺的技术比较。从图 13 可以看出,传统精炼工艺采用LF 炉加铝深脱氧, 不但增加了铝耗造成大量 Al2O3夹杂 ,而且无法实现真空下碳氧反应,只能发挥真空脱氢的简单功能 。而真空碳脱氧工艺可通过真空下吹氧脱碳和二次燃烧实现精炼过程热补偿, 同时利用真空下碳氧反应降低钢水氧含量 ,有利于减少铝加入量和降低 Al2O3 夹杂 ,有利于充分发挥真空冶炼的各种精炼功能。

4 .4 改变夹杂物上浮机制
传统洁净钢生产流程中常采用铝脱氧工艺, 生成的脱氧夹杂物大多为细小的 Al2O3 夹杂 。同时还原精炼过程中脱硫、炉渣和耐火材料还原以及卷渣等现象使钢水发生二次氧化生成大量细小弥散的 Al2O3 二次夹杂。因此 , 夹杂物去除速率可表示为 :

式中:
kO 为表观脱氧速度常数 , s-1。如图 15[ 6]、16[ 7] 所示 , 降低渣中(FeO +M nO)含量和提高熔池搅拌能 ε, 有利于提高 kO , 促进 Al2O3 夹杂上浮 。

RH 在真空下通过弱搅拌促进夹杂物上浮可避免二次氧化 ,因此 ,在相同的炉渣(FeO +M nO)含量下 kO 高于常压下吹氩弱搅拌 。说明 RH 内采用吹氩弱搅拌促进夹杂物上浮的效果优于 LF 炉。但RH 属于无渣精炼过程 , 只能依靠炉衬耐火材料吸附 Al2O3 夹杂 , 而真空下耐火材料的二次氧化加剧 ,熔池增氧速度升高, 又降低了去除夹杂物的能力 。
针对上述现象 , 日本 N KK 研究开发出 NKPREM法强化脱氧工艺。该工艺在钢水加铝脱氧后向熔池增氢至 10 ×10-6 左右,利用 RH 脱氢功能使钢水中的氢析出形成大量微小的氢气泡 ,从钢液内上浮并携带钢中大量细小 A l2O3 夹杂上浮。
如图 16 所示, NK-PREM 法的脱氧速度常数kO(图中黑点)高于传统吹氩搅拌法。从图 17[ 7] 可以看出 ,采用 N K-PREM 工艺处理后钢中不会存在5 ~ 10 μm 的大型夹杂 ,而小于2μm 的微细夹杂物含量也可降低 90 %。上述试验结果证明 ,改变夹杂物的上浮机制对于去除钢中夹杂物, 提高钢水洁净度具有明显的效果。
5 结论
1)洁净钢并非特指某一类具体的钢种, 而是代表实现生产过程中控制钢水洁净度所能达到的工艺水平。
2)以全量铁水“ 三脱” 预处理和转炉少渣冶炼工艺为基础的洁净钢生产新流程是今后洁净钢生产工艺的重要发展方向。
3)传统洁净钢生产流程存在以下基本矛盾 :炼钢回硫 ,低碳脱磷 ,铝脱氧与夹杂物控制和采用强还原精炼工艺 ,也是造成钢质量不稳定 、生产成本高、能耗高的主要原因 。
4)建立起高效低成本洁净钢生产技术平台需要进一步研究解决 :全量铁水“三脱”预处理、少渣冶炼 、高碳出钢和真空碳脱氧以及改变夹杂物上浮方式等关键技术。
参考文献:
[ 1] 雀部實.1983 年と1992 年に預測した日本の大量生産鋼の不純物精煉限界濃度の檢證[ J] .ふぇぅむ, 1999 , 4(8):36.
[ 2] 野崎努.底吹转炉法-引进· 搅拌效果· 顶底复合吹炼[ M] .张柏汀, 张劲松, 译.北京:冶金工业出版社, 2008.
[ 3] 岩瀨正則.制鋼スラゲ發生量抑制脱磷熱力學 のためのょ[ J] .-IS IJ, 1998 , 11:737
[ 4] 安井洁, 竹岡正夫, 宫島正和.脱りん銑を用ぃた轉爐操業技術[ J] .鐵と鋼, 1990(11):1908.
[ 5] 川上正博, 伊藤公允.复合吹炼转炉の冶金反应特性[ J] .ISIJ ,1990(11):1791.
[ 6] 小倉康嗣.二次精煉プロセスの開発と代酸素, 低硫鋼溶製法の確立[ J] .鐵と鋼, 1986(9):1309.
[ 7] Matsuno H , Kik uchi Y, Komatsu M , 等.RH 脱气装置脱氧新技术的开发[ J] .国外钢铁, 1994(5):26.